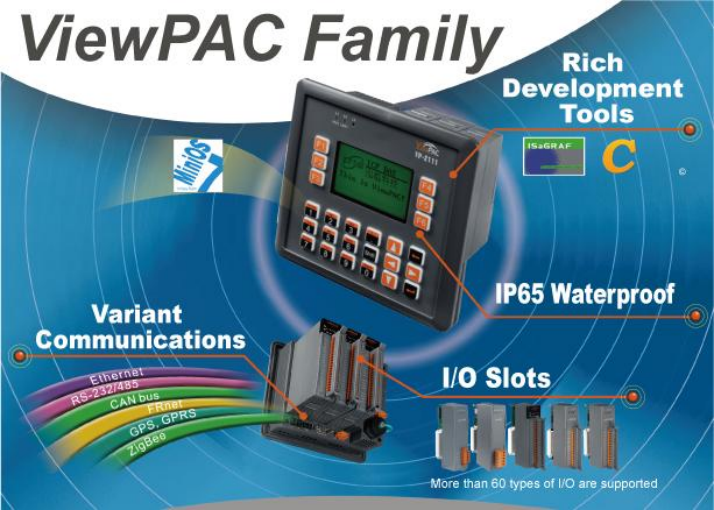
ViewPAC combines iPAC, a graphic display and keypad in one unit. It equips an 80186 CPU (16-bit and 80MHz) running a MiniOS7 operating system, several communication interfaces (Ethernet, RS-232/485), STN LCD and a rubber keypad. Its DOS-like operating system, MiniOS7, can boot up in a very short time (0.4~0.8 seconds). It has a built-in hardware diagnostic function. Compared to traditional HMI + PLC solutions, ViewPAC reduces overall system cost, space and gives you all the best features of HMIs and PLCs.
The VP-2111 series has a 16-bit CPU, 128 x 64 resolution graphic display, silicon rubber keypad, Ethernet, RS-232, RS-485 communication ports and 3 I/O expansion slots. It also equips a DOS-like OS called MiniOS7. Users can develop programs, use C compilers to create 16-bit executable files (*.exe) then download it to the controller. Turbo C 2.0 or Turbo C++ 1.0.1 can be used to compile application programs and generate execution files. The execution files can be download to VP-2111 via RS-232 or Ethernet port. We recommend Turbo C++ 1.01. There are many demo programs available for reference. For TCP/IP programming, we provide a TCP/IP server template named XServer. It is a very powerful, easy use and flexible tool that can save 90% development time.
Software Features
- MiniOS7 Embedded Operating System (DOS-like)
- C language Based Software Development Toolkit
- Modbus Library Provided
- Hardware Diagnostic Functions
- Load Files via RS-232 or Ethernet
HardwareFeatures
- 80186, 80 MHz CPU (16-bit)
- IP65 Compliant Front Panel
- STN LCD with Chinese Font
- Rubber Keypad with 24 Keys
- One 10/100M Ethernet Port
- 64-bit Hardware Serial Number for Software Protection
- Operating Temperature: -15 ~ +55 °C
|
||||||||
C Language Based ViewPAC (MiniOS7 Inside)
|
||||||||
Model | CPU | SDRAM | Dual Battery Backup SRAM | NAND Flash | Display Type | Ethernet Port |
RS-232/ RS-485 |
I/O Slot |
---|---|---|---|---|---|---|---|---|
VP-2111 | 80186 or compatible, 16-bit and 80 MHz | 768 KB | 512 KB | 64 MB | STN, 128x64 Dot Matrix LCD | 1 | 3 | 3 |
There are two types of I/O communication bus, parallel bus and serial bus. The parallel bus type I/O modules (high profile I-8K series) are high speed ones used only in the PACs including XPAC, WinPAC, iPAC, ViewPAC, etc. And the serial bus type I/O modules (high profile I-87K series) are low speed ones used in both PACs including XPAC, WinPAC, iPAC, ViewPAC, etc., and I/O expansion units including RU87Pn, ET-87Pn, USB-87Pn, etc.
The differences between the two series are listed as follows:
Model | I-8K Series | I-87K Series |
---|---|---|
Communication Interface | Parallel Bus | Serial Bus |
Protocol | - | DCON |
Communication Speed | Fast | Slow |
DI with Latched Function | - | Yes |
DI with Counter Input | - | Yes (100 Hz) |
Power on Value | Yes | Yes |
Safe Value | Yes | Yes |
Programmable Slew-Rate for AO Module | - | Yes |
For more information, please go to the following web page.
Remote I/O Selection
Ethernet
The available Ethernet I/O devices are ET-7000, ET-7200, ET-87P4/8-MTCP and I-8KE4/8-MTCP. The PAC can access them in Modbus/TCP protocol. A nModbus.dll is provided for C#, VB.net programming.
RS-485
The PACs are equipped with the RS485 COM ports which enable the transmission rate up to a maximum of 115.2 Kbps. The medium for connection is a twisted-pair, multi-drop, 2-wire RS-485 network that can link I-7000, M-7000, RU-87Pn with high profile I-87K modules. To access M-7000, a nModbus.dll is provided for C#, VB.net programming. To access I-7000 and RU-87Pn with high profile I-87K modules, PACSDK is provided for C#, VB.net, VC and VB programming.
FRnet
FRnet is an innovative industrial field bus that has many special features, such as high-speed deterministic I/O control, real I/O synchronization capabilities, non-protocol communication, and easy programming. With a FRnet communication module (I-8172W), the PAC can link FRnet I/O modules to implement high-speed distributed I/O (FR-2000 series). To access I-8172W, a pac_i8172w.dll is provided for C#, VB.net, VC and VB programming.
CAN Bus
The Controller Area Network (CAN) is a serial communication way, which efficiently supports distributed real-time control with a very high level of security. It provides the error-processing mechanisms and concepts of message priority. These features can improve the network reliability and transmission efficiency. Furthermore, CAN supplies the multi-master capabilities, and is especially suited for networking“intelligent” devices as well as sensors and actuators within a system or a sub-system. With I-8123, I-8124, I-87120, the PAC is able to demonstrate every feature of CAN, CANopen, and DeviceNet.