-
OPC UA I/O Modules
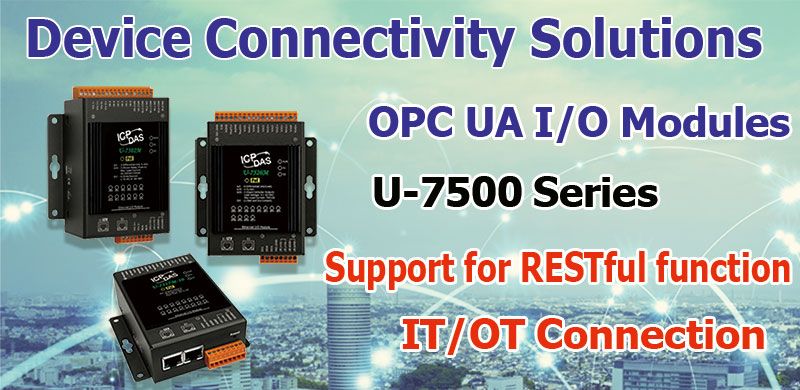
OPC UA I/O module is a series of IIoT Ethernet I/O modules, known as UA I/O or U-7500 Series. It has a built-in dual-port Ethernet switch to implement daisy-chain topology. The cabling is much easy and can reduce the total cable and switch cost. It follows IEEE 802.3af (Class 2) compliant Power over Ethernet (PoE) specification. It allows receiving power from PoE enabled network by Ethernet pairs. This feature provides greater flexibility and efficiency to simplify system design, save space, and reduce wirings and power sockets.
In industrial communication, UA I/O supports the OPC UA Server / Client and MQTT Client and RESTful API communication functions (and can be used simultaneously). Users can choose the networking mode according to their needs and environment, to transmit the values of built-in I/O channels to the Cloud system or field control system for displaying, analysis or strategy. Support Scaling. Let the analog signal be converted into a more readable value. Support logic function rule setting IF, THEN, ELSE, can set up logical condition/action for I/O and virtual point; Provide schedule function to execute the set rules at a specific time; and support RESTful API function, can read/write I/O and virtual point through HTTP or HTTPS(identity verification and communication encryption).
In the information security and data security of the platform connection method, the following functions are provided respectively to enhance the security of I/O networking:
Connectivity for various platforms | OPC UA, MQTT, RESTful API can be used simultaneously |
---|---|
Connect to Cloud | OPC UA, MQTT |
Connect to SCADA | OPC UA, MQTT |
Connect to MES | OPC UA |
Connect to IT | MQTT, RESTful API (HTTP, HTTPS) |
Security | I/O Networking Security Functions |
---|---|
Information Security | HTTPS, Port Binding, Allowlist, ICMP drop |
Data Security | Certificate(X.509), Communication Encryption(SSL/TLS) |
UA I/O Series provides a Web-based User Interface (Web UI) to configure the module, control the output channels, monitor the connection, and I/O status via a normal web browser. It is easy, fast, and no extra APP needed.
OPC UA Architecture:
MQTT Architecture:
Features
-
Built-in OPC UA Server Service
Compliance with IEC 62541 Standard. Provides functions of Active Transmission, Transmission Security Encryption ( SSL / TLS ), User Authentication (X.509 Certificates / Account password), Communication Error Detection and Recovery, etc. to connect SCADA or OPC UA Clients. Recommend to keep the maximum number of sessions within 3 connections.
- Built-in OPC UA Client Service
Compliance with IEC 62541 Standard. Provides Transmission Security Encryption ( SSL / TLS ), User Authentication (X.509 Certificates / Account password) and OPC UA Server Connectivity.
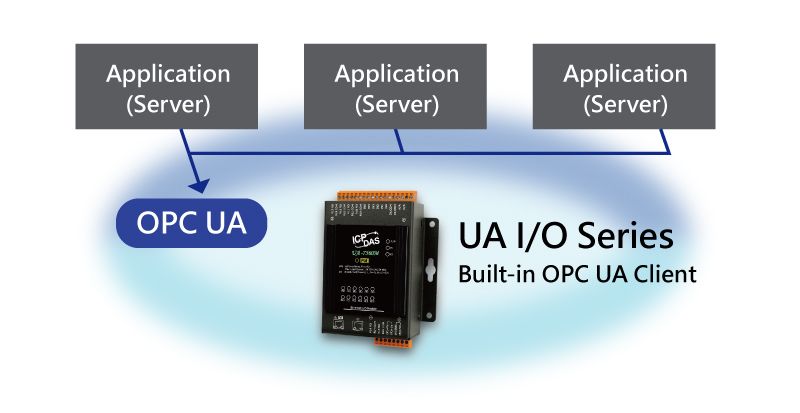
- Built-in MQTT Client Service
Build-in MQTT Client Service (Compliance with MQTT V.3.1.1 protocol). Provides functions of IoT Active M2M Transmission, QoS (Quality of Service), Retains Mechanism, Identity Authentication, Encryption, Last Will, etc.
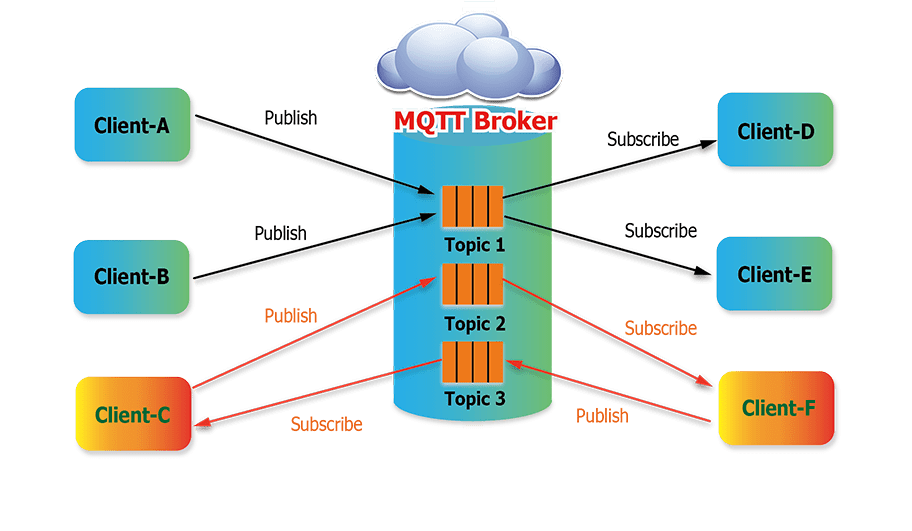
- RESTful API
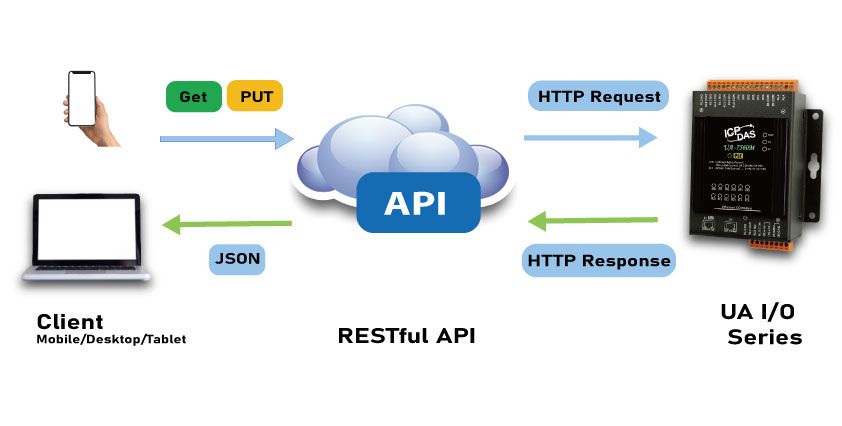
-min.png)
- Execute OPC UA , MQTT, and RESTful API Communication at the Same Time
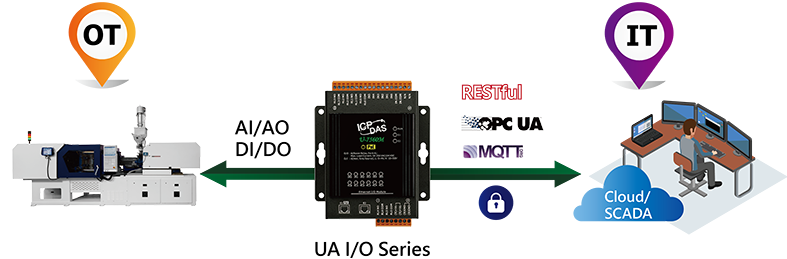
- Support IoTstar Cloud Management Software
UA I/O factory version 9.7 and later supports this function.
1.jpg)
- Scaling Function for Improved Readability
AI/AO modules support Scaling. Let the analog signal be converted into a more readable value.
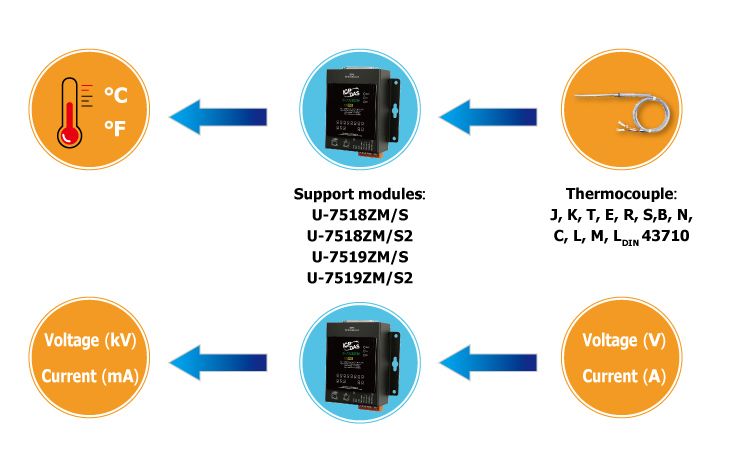
- Support Logic Function Rule Setting: IF, THEN, ELSE
Users can set up logical condition/action for I/O and virtual point.
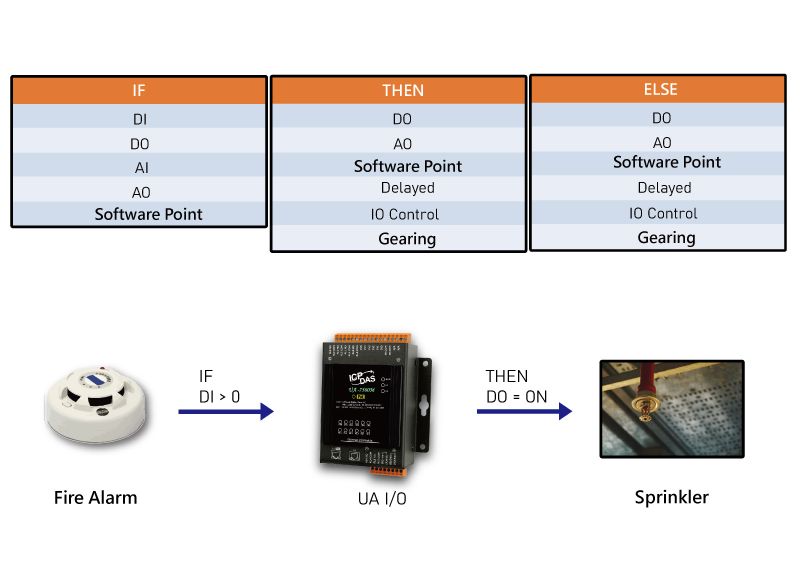
- Support Schedule
Provide schedule function to execute the set rules at a specific time.
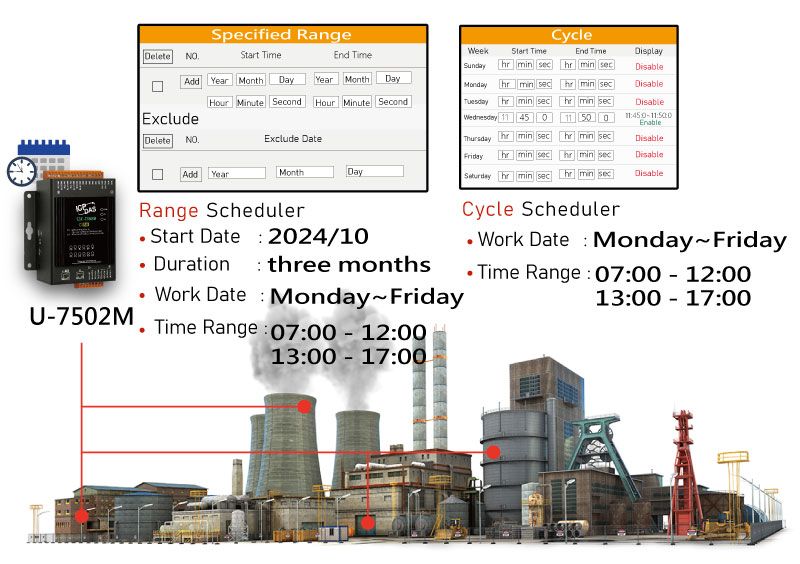
- Support Event Log
When the I/O value changes, record the current I/O value for easy device tracking in the future.
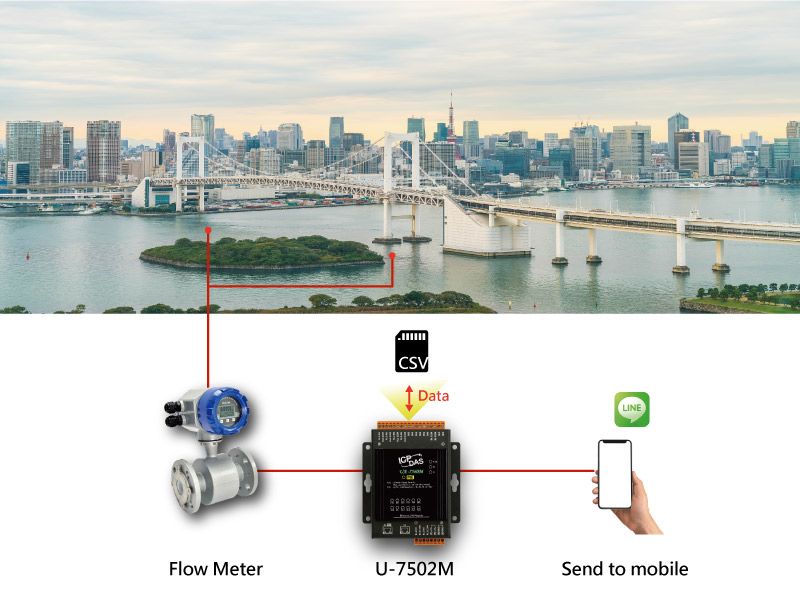
-
Built-in Web Server to Provide the Web User Interface
UA I/O Series provides a Web-based User Interface (Web UI) to configure the module, control the output channels, monitor the connection, and I/O status via a normal web browser. It is easy, fast, and no extra APP needed.
-
Diversified Choices
Different models provide different AI, AO, DI, or DO channels, and users can choose the desired model according to the needs of the case.
-
Dual-port Ethernet Switch for Daisy-Chain Topology
The cabling of Daisy-Chain Topology is much easier and total costs of cable and switch are significantly reduced.
-
IEEE 802.3af-compliant Power over Ethernet (PoE)
UA I/O follows IEEE 802.3af (classification, Class 2) compliant Power over Ethernet (PoE) specification. It allows receiving power from PoE enabled network by Ethernet pairs. This feature provides greater flexibility and efficiency to simplify system design, save space, and reduce wirings and power sockets.
Advantages
-
Selection Guide
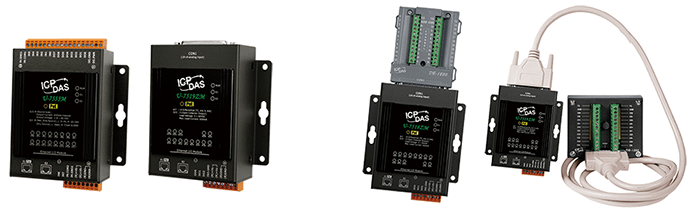
|
||||||||
OPC UA I/O Modules
U-7000 Series: Built-in with the OPC UA Server and MQTT Client services
|
||||||||
Module | AI | AO | DI | DO | ||||
---|---|---|---|---|---|---|---|---|
Ch. | Type | Ch. | Type | Ch. | Type | Ch. | Type | |
U-7502M | 3 | ±150 mV, ±500 mV, ±1 V, ±5V, ±10V, +0 mA ~ +20 mA, ±20 mA, 4 ~ 20 mA |
- | - | 6 | Wet (Sink,Source) | 3 | Power Relay Form A (SPST N.O.) |
U-7504M | 4 | ±500mV, ±1V, ±5V, ±10V, 0~20mA, ±20mA, 4~20mA |
4 | 0~5V, ±5V, 0~10V, ±10V, 0~20mA, 4~20mA |
4 | Dry (Source), Wet (Sink) |
- | - |
U-7515M | 7 | Pt100, Pt1000, Ni120, Cu100, Cu1000 |
- | - | - | - | - | - |
U-7517M | 8 | ±150 mV, ±500 mV, ±1 V, ±5 V, ±10 V ±20 mA, 0 ~ 20 mA, 4 ~ 20 mA |
- | - | - | - | 4 | Isolated Open Collector (Sink) |
U-7517M-10 | 10/20 | ±150mV, ±500mV, ±1V, ±5V, ±10V, ±20mA, 0~20mA, 4~20mA |
- | - | - | - | - | - |
U-7518ZM/S | 10 | ±15 mV, ±50 mV, ±100 mV, ±500 mV, ±1 V, ±2.5 V, ±20 mA, 0 ~ 20 mA, 4 ~ 20 mA Thermocouple: J, K, T, E, R, S, B, N, C, L, M, LDIN43710 |
- | - | - | - | 3 | Isolated Open Collector (Sink) |
U-7518ZM/S2 | ||||||||
U-7519ZM/S | 10 | ±15mV, ±50mV, ±100mV, ±150mV, ±500mV, ±1V, ±2.5V, ±5V, ±10V, ±20mA, 0~20mA, 4~20mA Thermocouple: J, K, T, E, R, S, B, N, C, L, M, LDIN43710 |
- | - | - | - | 3 | Isolated Open Collector (Sink) |
U-7519ZM/S2 | ||||||||
U-7524M | - | - | 4 | 0~5V, ±5V, 0~10V, ±10V, 0~20mA, 4~20mA |
5 | Dry (Source) Wet (Sink) |
5 | Isolated Open Collector (Sink) |
U-7526M | 6 | ±500 mV, ±1V, ±5V, ±10V, 0~20mA, ±20mA, 4~20mA |
2 | 0~5V, ±5V, 0~10V, ±10V, 0~20mA, 4~20mA |
2 | Dry (Source) Wet (Sink) |
2 | Isolated Open Collector (Sink) |
U-7528M | - | - | 8 | 0~5V, ±5V, 0~10V, ±10V, 0~20mA, 4~20mA |
- | - | - | - |
U-7542M | - | - | - | - | - | - | 16 | Isolated Open Collector (Sink) |
U-7544M | - | - | - | - | 8 | Wet (Sink,Source) | 8 | Isolated Open Collector (Sink) |
U-7545M | - | - | - | - | - | - | 16 | Isolated Open Collector (Source) |
U-7550AM | - | - | - | - | 12 | Dry (Source) Wet (Sink) |
6 | Isolated Open Collector (Sink) |
U-7551M | - | - | - | - | 16 | Wet (Sink,Source) | - | - |
U-7552M | - | - | - | - | 8 | Wet (Sink,Source) | 8 | Isolated Open Collector (Source) |
U-7553M | - | - | - | - | 16 | Dry (Source) | - | - |
U-7555M | - | - | - | - | 8 | Dry (Source), Wet (Sink,Source) |
8 | Isolated Open Collector (Source) |
U-7558M | - | - | - | - | 8 | Wet (Sink/Source) | - | - |
U-7559M | - | - | - | - | 8 | Wet (Sink/Source) | - | - |
U-7560M | - | - | - | - | 6 | Wet (Sink/Source) | 6 | Power Relay Form A (SPST N.O.) |
U-7561M | - | - | - | - | - | - | 11 | Power Relay Form A (SPST N.O.) |
U-7567M | - | - | - | - | - | - | 8 | Power Relay Form A (SPST N.O.) |
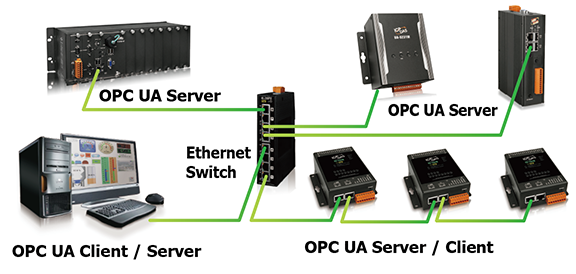
-
OPC UA
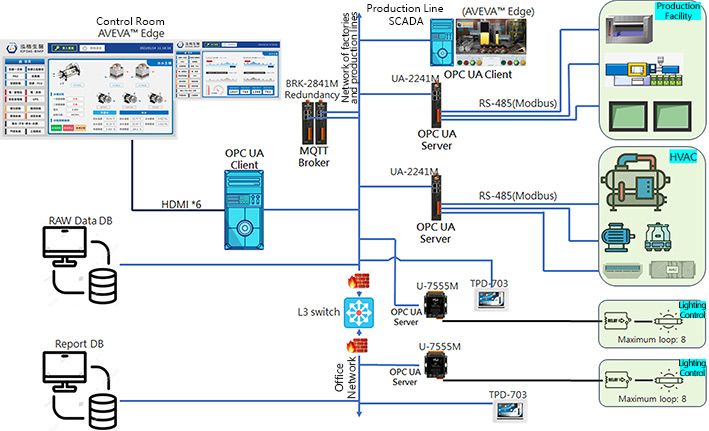
The main purpose of the Control Room SCADA is to provide visual information to plant managers to maintain the normal operation of the plant. Designed and deployed with AVEVA™ Edge, the Control Room SCADA can present real-time information and images of production lines, plant services, IP equipment security topology, and cameras, and display alarm messages when equipment is out of order, allowing managers to quickly troubleshoot abnormalities. In addition, the storage and utilization of real-time information is also an important function of the Control Room SCADA. The source of real-time information in the plant and production of the Control Room SCADA is obtained through the OPC UA protocol of TCP/IP, which is different from the map control architecture that uses Modbus TCP protocol, and the following is a list of the common differences of the protocols.
- OPC UA has two communication modes, Client/Server and Publish-Subscribe, while Modbus uses a One Question One Answer Client/Server architecture for communication.
- OPC UA incorporates security features like encryption, authentication, and access control, whereas Modbus does not.
- Modbus is designed for industrial control systems and is typically used to access data from devices like programmable controllers, drives, and sensors.
- OPC UA communicates based on the TCP/IP protocol, can be deployed on any hardware and software platform that supports this protocol and can interact with a variety of devices and systems regardless of their manufacturer or location. In comparison, Modbus is designed to work with a limited number of devices and systems that support the Modbus protocol.
The UA-2241M UA communication server, in this case, collects the data of the production line and factory equipment and then converts it to OPC UA protocol before providing it to the Control Room. There are two main benefits of switching to the OPC UA protocol, one is to reduce the number of communication packets, and the other is to ensure the security of data transmission at the TCP layer.
The UA I/O series U-7555M is used for factory lighting control. In addition to the advantages of the OPC UA protocol mentioned above, it also utilizes the logic control within the UA I/O to determine the actual on and off status of the lights, reducing the need to write development logic for the TPD-703. In addition, the scheduling function of the UA I/O can also schedule the factory lights to be turned off, avoiding the situation where the lights are not turned off during off-duty hours.
Ans: OPC UA Client is an application program that connects to the OPC UA Server and reads data. OPC UA Client is designed to communicate with a common industrial automation protocol called "OPC UA". The purpose of this protocol is to gain interconnectivity between different systems (e.g. workstations, tools, production machines, etc.) so that they can be exchanged and controlled within the same system. The main function of the OPC UA Client is to read data (e.g. sensor data, production data, etc.) from the OPC UA Server and display it in a readable form on the user interface.
OPC UA Client can fulfill the needs of the following systems, devices, or scenarios:
A. Industrial Automation Systems B. Smart Homes C. Micro Controllers D. IoT Systems E. Monitoring and Control Systems F. Production Automation Systems
Since the OPC UA Client can read and display data from many devices and equipment, it can be used as a cross-platform and cross-device data display application that is compatible with the latest industry standards. Before setting up an OPC UA Client, it is important to ensure that the communication adapter associated with the client is connected to the OPC UA Server to be accessed, which is usually a data network based on a computer networking protocol such as TCP/IP. By configuring the necessary connection parameters (e.g. URL, exchange protocol, etc.), the client can connect to Server.
Ans: OPC UA Server is an application program that provides data and information and is the core of OPC UA technology. In OPC UA, it is responsible for managing, collecting, storing, and distributing data. The role of OPC UA Server is similar to that of a hub controller, which can be connected to a variety of different clients to provide data access and exchange.
The main task of the OPC UA Server is to manage the data model, which describes the relationships between the different data items in the system. By integrating data into a unified data model, OPC UA Server can acquire data from a variety of different data sources. For example, an OPC UA Server can take data from PLCs, meters, sensors, and other devices, convert it to a uniform data format, and send it to the client.
In addition, the OPC UA Server is responsible for security and privilege management. It can ensure the security of data in the transmission process through encryption, access control, and authentication mechanisms. In addition, users can assign different privileges to different users through privilege management to protect the security of data.
Ans: The Client/Server communication model of OPC UA is the traditional communication architecture of OPC. The process starts with the Client sending a connection request to the Server, and then the Server verifies the identity and responds with the connection result. When the Client needs to get data from the Item on the Server side, it can send a request to the Server to subscribe and monitor the Item data, and when there is a change in the data on the Server side, it will actively respond to the Client, and when the Client needs to change the Item data, it needs to actively send a data write request to the Server, and the Server will respond to the right result. The Server will respond with the written result.
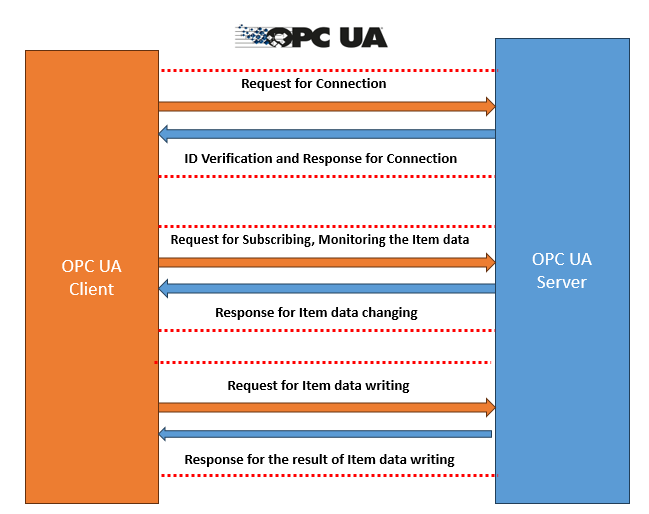
Company | Client Name | Platform | License | Download link | Last version |
---|---|---|---|---|---|
Unified Automation | UA Expert | Windows | Free | http://bit.ly/UaExpert | 1.7.0 (2023-07-13) |
Prosys | OPC UA Browser | All (java) | Free | http://bit.ly/ProsysOpcUaClient | 4.4.0 (2022-11-28) |
Softing | OPC UA Demo-Client | Windows | Free | http://bit.ly/SoftingOpcUa | 2.30.0 (2022-01-13) |
Free OPC UA | OPC UA Client GUI | All (Python) | Free | http://bit.ly/FreeOpcUA | 0.8.4 (2022-01-31) |
Kepware | OPC UA Client Driver | Windows | Commercial | http://bit.ly/KepwareOpcUa | |
Node OPC UA | OPC UA Commander | All (JS) | Open-source | http://bit.ly/NodeOpcUaClient | 0.31.0 (2023-07-20) |
UA I/O Series | UA Communication Server | |||
---|---|---|---|---|
U-7000 Series | UA-2841M | UA-5231/UA-2241 Series | UA-7231M | |
OPC UA Server Session | 3 | 50 | 20 | 20 |
OPC UA Client Session | 1 | unsupported | unsupported | unsupported |
UA I/O Series | UA Communication Server | |||
---|---|---|---|---|
U-7000 Series | UA-2841M | UA-5231/UA-2241 Series | UA-7231M | |
OPC UA Server | O | O | O | O |
OPC UA Client | O | X | X | X |
MQTT Broker | X | O | O | O |
MQTT Client | O | O | O | O |
MQTT JSON | O | O | O | O |
Modbus RTU Master | X | O | O | O |
Modbus TCP Master | X | O | O | O |
EtherNet/IP | X | O | O | O |
SNMP V3 Agent | X | O | X | X |
RESTful API | O | O | X | X |
Remote SQL Data Log | X (Note 1) | O | O | O |
Local Data Log | O | O | O | O |
IFTTT | X | O | O | O |
IoTstar | O | X | X | X |

This application has been adopted by many petrochemical industries and is working well.
Ans: Please refer to the following link for the operation of different devices and databases.
https://www.icpdas.com/en/faq/index.php?kind=326#950
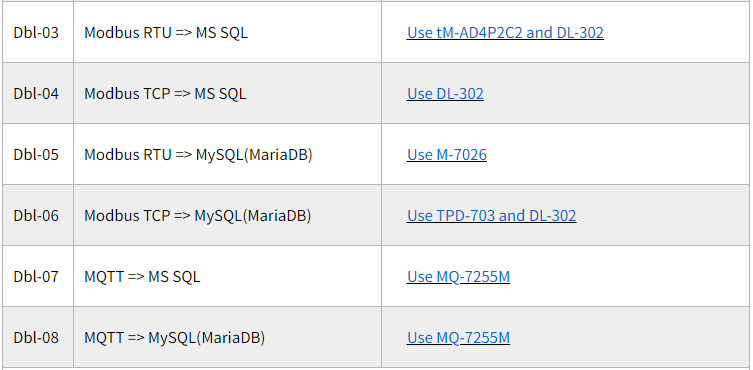
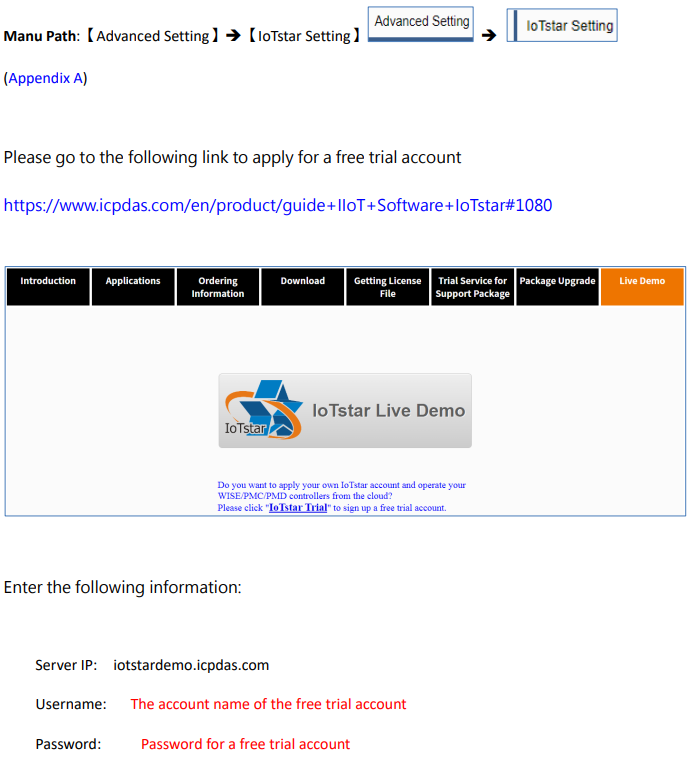
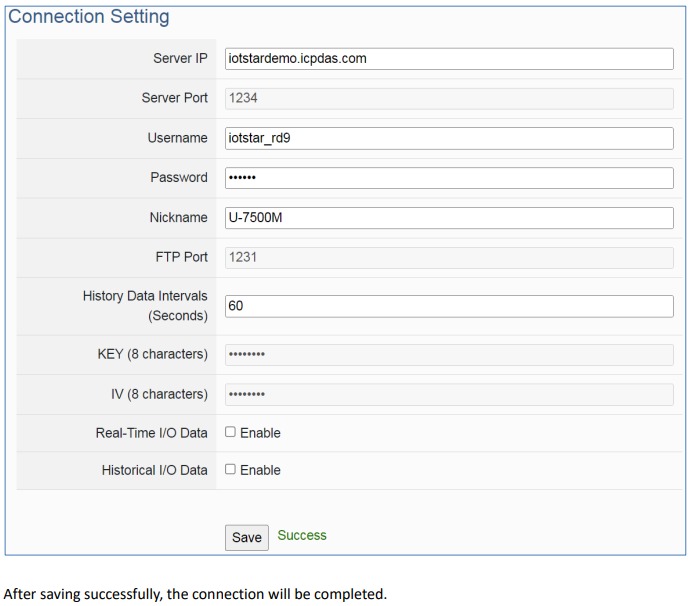
-
OPC UA I/O Module: U-7500 Series Applications
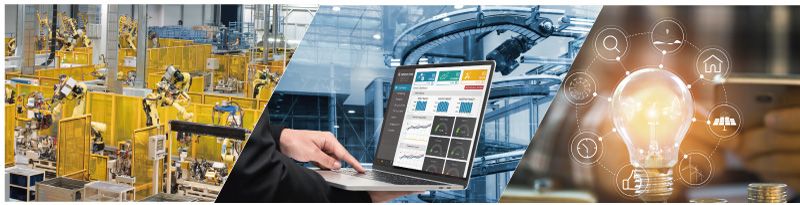
[Customer Needs]
1. Monitoring the motor special-output current in the factory
2. High security data transmission
3. Monitor the factory through wireless according to the client's needs
1. Designed to monitor the special-output current motor in the factory
The input of the electric meter is 50 / 60 Hz, and the output of the motor in the field is 50 / 6000 Hz, the precision is not enough to use an electric meter for motor monitoring, therefore, a high-frequency CT is used to monitor the motor output current.
2. Enhanced data transmission with high security
The U-7500 series modules transfer the motor current data through OPC UA and MQTT protocols with high security, so the information security of the factory can be improved.
3. Monitoring the client's factory via wireless
Through the RJ45 to Wi-Fi adapter, the wired signal in the factory is converted to wireless signal transmission, allowing customers to monitor the factory.
[ UA I/O Module Motor Monitoring Framework]:
Using ICP DAS IoTstar with UA I/O solution can bring many benefits. In this case, the customer uses IoTstar cloud management software combined with UA I/O module series to set up a cloud IoT monitoring system, and the manager can get the following benefits.
** Support IoTstar cloud management software
1. No programming is required
Collect environmental parameters and store them in the cloud database, the system can be set up through the web interface without writing programs.2. Collection and monitoring of production line information
Check environment parameters of the site in real-time via IoTstar Dashboard Service, information on the production line can be collected and monitored completely.
3. Reduce the cost of equipment maintenance
Through IoTstar Remote Access Service, cloud monitoring, setting adjustment, and firmware updates can be performed, reducing the time and cost of personnel movement due to equipment maintenance.
[ IoTstar with UA I/O Module Environmental Monitoring Framework]:
Various smart devices have been added to daily life. Smart lighting control can achieve energy savings, data analysis, and remind maintenance of lighting equipment. However, it also faces the threat of security attacks. ICP DAS has installed an intelligent lighting control system to provide stable lighting and arrange maintenance to reduce management costs.
The new function reduces the distance between the new technology and people by retaining the traditional light control panel switch. It provides the service when the lighting control moduleneeds to be repaired. The security of data transmission using the network interface for lighting control also needs to be considered.
System Architecture
ICP DAS on the lighting control system for medical factorys, in addition to the traditional lighting and physical switches, six additional units have been added, a lighting control panel, network switch, touch screen, communication server, factory monitoring system, and monitoring and early warning system.
The lighting control can also be integrated with various sensors to realize context-based dimming functions to achieve energy-saving effects, and data analysis can be added to remind equipment maintenance to reduce management costs.
1. Lighting Control Panel
The control core is the U-7555M module. The digital outputs and inputs on the module are wired to the relays of the lighting circuits and the lighting panel switch, respectively. This module also provides logic and scheduling control. It's a stand-alone lighting control module. Provides three highly secure data exchange protocols, OPC UA, MQTT, and Restful API (https) to reduce information security risks.
2. Network Switch
The network switch is daisy-chained to the U-7555M in the lighting control panel, the user expects to install the touch screen on the cubicle wall and integrated it into the main network. The communication protocols are not polling mechanisms, the bandwidth requirements for the factory are extremely low.
3. Touch Screen
The touch screen is available in 2.8", 4.3", or 7". Small size fi ts only light switches, large size with other settings that can be integrated, such as air conditioning, access control, power information, environmental sensor information,etc. It can also use a control interface for lighting and air conditioning.
4. Communication Server
BRK-2841M provides the Broker function of MQTT protocol for MQTT message dispatching and proxy. It is compliant with MQTT V.3.1, 3.1.1, and 5.0 protocols, and supports the QoS message quality mechanism, retention mechanism, identity verifi cation, communication encryption, Last Will, and bridging function. Supports Web UI setting to quickly set up the BRK function, which can reduce the burden of setting up the Broker by individuals and reduce management costs. Itprovides clustering, bridging, load balancing, and high availability functions to prevent service downtime due to system failure in the field.
5. Factory Monitoring System
Using AVEVA Edge to integrate water, electricity, gas, lighting, access control, etc. within the factory. Provides the information in real-time on factory computers, handheld devices, and databases where information is not immediately available but needs to be stored. The former provides a stable production environment, while the latter is used for data analysis and supplied maintenance notification, etc.
6. Monitoring and Early Warning System
The network planning is based on the Purdue model of IoT, but most of the equipment purchased in the factory cannot provide high-security communication protocols. Therefore, a monitoring and early warning system is built to monitor IP and devices without encrypted communication protocol (Modbus TCP) in the factory in real-time, and notify MIS, factory management and record notification in case of abnormalities.
Due to labor costs increasing and manpower shortages in the manufacturing industry, how to digitize information is an important issue, companies have trouble integrating IT and OT staff because they have different perceptions, and eventually have to abandon the project. The difficulties, in this case, can be divided into the following items:
1. Hard to record Sensor value
2. Machine messages scattered
3. No Data Graphing
ICP DAS uses the U-7526M to convert analog signals into RESTful API / MQTT data to achieve the goal of "information digitization". Makes it more flexible for database and graphic software and makes it easier to control and record.
Advantages of ICP DAS:
1. Digitalization for recording2. Centralized message
3. Data graphing
Architecture of ICP DAS:
Integrate sensing and output modules to simplify difficulties in the field
The reverse osmosis equipment encountered the problem that no space to place the sensor module and the controller, the U-7526M provides analog sensor and OPC UA services to collect water quality, flow, and pressure data from equipment to the IT system, reducing field staffing integration burden.
ICP DAS U-7500 Series is used in a wide range of applications in commercial buildings and can effectively integrate various facilities for automation management:
Lighting Scheduler
Commercial buildings have huge lighting needs. The U-7500 Series not only controls the lighting in the building but also monitors the lighting status of the building and saves energy by automatically switching off the lights in unoccupied areas with devices such as motion sensors. The system also supports a preset Scheduler, for example, at night or in public places, to automatically switch on and off the lights according to the schedule, reducing the complexity of staff operation.
Ventilation Monitoring
The U-7500 Series can also monitor and manage the ventilation system in commercial buildings. By connecting to CO2 sensors or air quality sensors, the system can automatically adjust the operation of the ventilation fans to ensure that the indoor air quality is up to standard. In crowded areas, the system will increase the number of air changes while reducing the ventilation operation in unoccupied areas, which ensures a comfortable environment and reduces operating costs.
Send Messages To Line
The U-7500 Series can monitor the status of various building equipment in real-time, such as lighting systems, ventilation systems, environmental sensors, etc. If the system detects a fault or environmental data outside the default range, the module will automatically trigger an alarm and notify the staff via Line.
[ Commercial Building Application Framework ] :
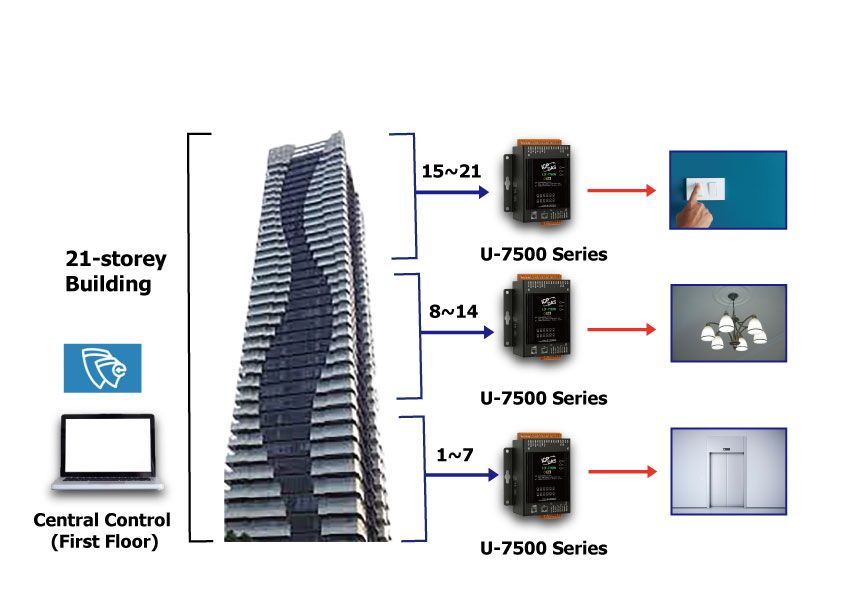
Live Demo of OPC UA I/O Module
-
U-7526M UA I/O Module
Username: root
Password: root