Search: Product Update
Application for Generator Management System in Taipei 101 Building
Product Update
2015-06-26
The generator management system provides full range of control and management of the generators; the SCADA system with user-friendly interface is designed for easy operations. The system architecture adopted coherent communication, therefore when new features is added in the future, as long as the module or hardware uses the same communication, the new features can be seamlessly added without affecting the existing architecture. The distributed modules can function independently to acquire hardware status information, and can be replaced without shutting down the system.
System Architecture
A. Hardware
- WinPAC programmable controller
The generator management system is designed to receive data from the front-end modules through Modbus protocol (protocol commonly used in industrial applications) via RS-485, and then actively transfer the data to the back-end graphic control via Ethernet for data gathering. The following figure shows the general specifications of WinPAC.
- M-7051D - 16-channel Isolated Digital Input Module with Display
M-7051D is a module for front-end data acquisition. In this case, it will receive the digital signals of the sensors from the generator devices or the peripherals devices of the generator, and send back these data such as: the error status and operation status of the generator, and the high/low voltage of the battery, etc. via RS-485 to the WinPAC controller. The following figure shows the specifications of the M-7051D:
- M-7017Z-10/20-channel Analog Input Module with High Voltage Protection
M-7017Z is a module for front-end data acquisition. In this case, it will receive the analog signals of the sensors from the peripherals devices of the generator, and send back the data such as: the liquid level of the oil tank via RS-485 to the WinPAC controller. The following figure shows the specifications of the M-7017Z:
B. Software
Software Architecture
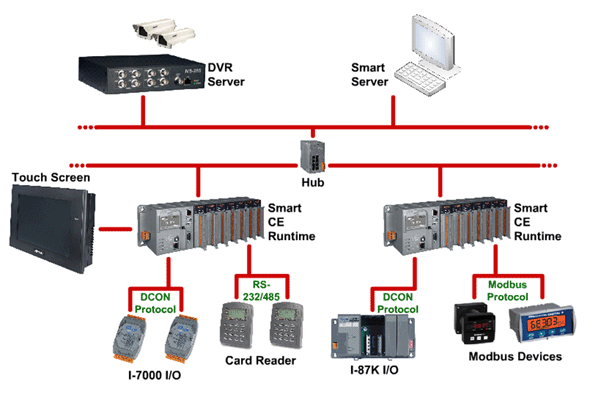
- Smart CE Runtime(Distributed and Independent Operation)
Smart CE Runtime is able to collect information of the WinPAC module and the expansion module. It can process I/O logic and provides a simple HMI for display, please refer to the following link for the devices that is currently supported: http://smart.icpdas.com/smart4/spec.htm - Smart Server
Smart Server can connect to multiple Smart CE Runtimes, so the information for each Smart CE Runtime can be shown on the PC in real time as event alarms. The users can design customized HMI, record the events for management, review, and report generation, etc. 6 levels of access control with different authorities can be set for the users. And it can also connect to video recorders such as: DVR and NVR, etc., when an event occurs, the related scene can be displayed accordingly. Please refer to the following link for the video reorders that is supported currently: http://smart.icpdas.com/smart4/spec.htm
C. System Architecture
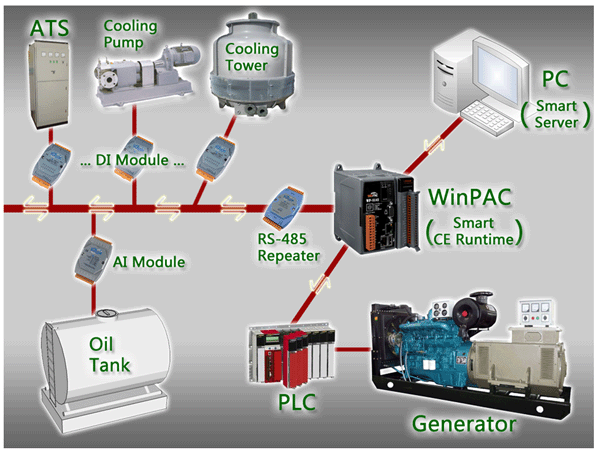
D. Network System
- Monitoring Loading/Unloading System
The loading/unloading information of the system can be sent to the WinPAC by Quantum PLC via Modbus RTU protocol. The Smart CE Runtime software on the WinPAC will take care of all of the received information and send them to the PC (with Smart Server installed) for further analysis for graphic control display and management.
- Monitoring Information of ATS, Cooling Pump, Cooling Tower, Oil Tank
The hardware status information can be received by the distributed modules such as I-7051D, I-7017Z ... etc., and then can be sent to the WinPAC via RS-485. The Smart CE Runtime software on the WinPAC will take care of all of the received information and send them to the PC (with Smart Server installed) for further analysis for graphic control display and management.
- Benefits for Using WinPAC(Smart CE Runtime) as Centralized Data Acquisition
In the past, the data acquisition for PLC is usually performed by PC. And each time when the PC crashes, the users will be difficult to get the real-time information of the devices. And generally the PC tends to increase the risk of crashes as the time of use increases; it is quite risky.
WinPAC is industrial level computer that is able to survive in harsh environments, it is relatively stable comparing to the PC. In this case, the WinPAC can be used for the data collection; and the Smart CE Runtime on the WinPAC will provide a basic HMI for user to view the information, when the PC experience a crash, the WinPAC can still function normally and the user can view the data from the HMI provided by WinPAC without missing any important information. After the PC is resumed and connected to the network, it can seamlessly take over the management and display of the data immediately.
Extensibility
A. The same communication protocol is used for easily adding new features if required The same communication protocol is used in this system, therefore if required; it is easy to add new features to the system without modifying the existing system as long as the newly added modules or hardware support the same communication protocol.B. Modularized design for easy maintenance and expansion
The information of hardware status can be acquired by the distributed modules. For the functionality of each distributed module is independent, if one module is damaged, it can be replaced directly without affecting the operation of the existing system. The users can also freely choose different modules that are specifically designed for different functionality when adding new features to the system, and the newly added modules can be immediately accessed via the existing network.
C. Expansion Suggestions
1. GSM module
In the conventional architecture, the information is always acquired via viewing HMI on the PC. When the user is away from the PC, they can’t get the latest information. In addition, the system won’t automatically send out the information therefore when unusual events occur, the user may not be able to get the important information in real time.
Nowadays, almost everyone has a cell phone, and the pervasive nature of cell phones brings real-time access to information in automation applications. With the GSM module, the user can preset to send messages right away when unusual events occur. The related personnel can be notified in real time for immediate response.
2. ZigBee Wireless Module
Wiring deployment is always a big issue when upgrading the old systems to new ones or when adding new functions to an existing system. Especially in harsh environments where wiring deployment is extremely difficult and may be expensive; with wireless modules such as ZigBee modules, the wiring problems can be easily solved and the cost can be reduced.
- ZigBee I/O Module
The information of the status of the devices are acquired and then transmitted via ZigBee module.
- Zigbee Converter Module
The ZigBee communication can be transferred to standard RS-485 protocol by using Zigbee Converter Module.
- ZigBee Repeater Module
The ZigBee Repeater Module can be used to reduce the noise and strengthen the signal.
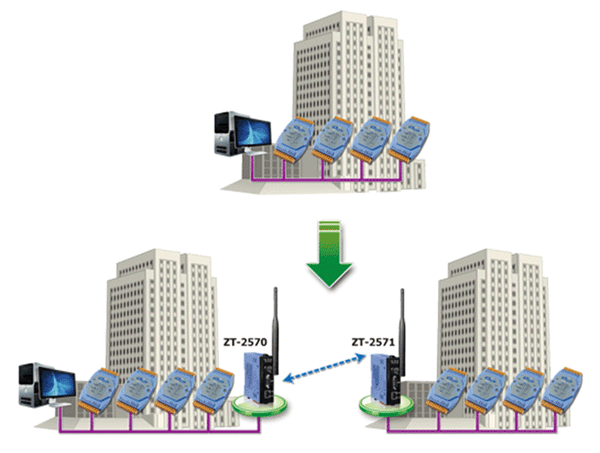
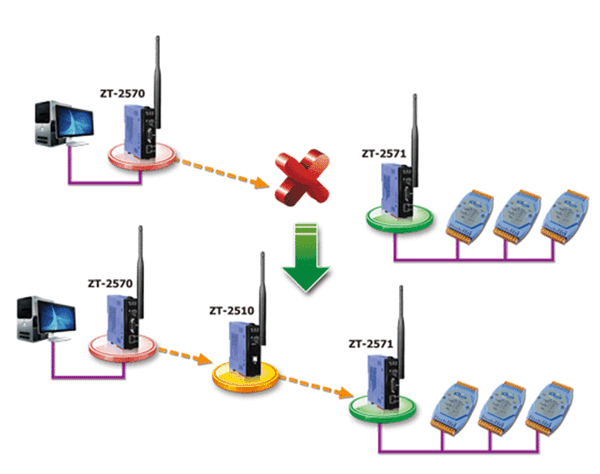
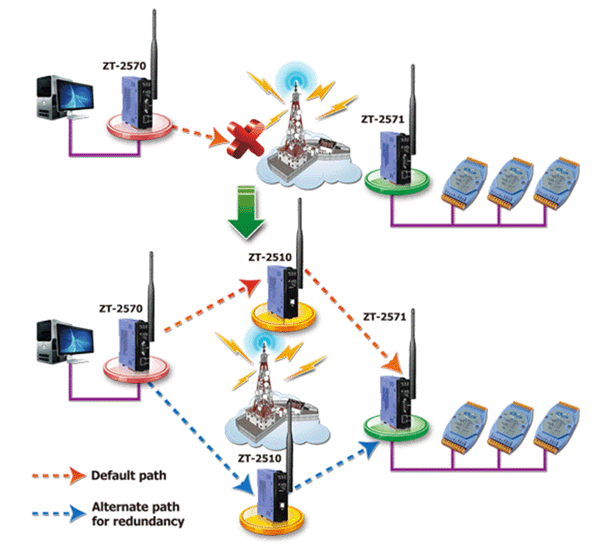